Pet Food Making Line
The production process:
Extrusion of petfood
Petfood processing focuses on the production of feeds for ani-mals with a high emotional value but low economic usefulness. Nonetheless, balancing the components and gentle processing are at the center of the related quality considerations. Extrusion is therefore increasingly proving to be the right tool for modern Petfood.
Extrusion process
In the extrusion process, a cooking operation follows the spe-cific processing of the raw materials by blending, mixing and grinding. The goal is essentially to achieve the following effects:
• Modification the starch
• Denaturation of proteins
• Shaping, expansion, texturing
• Improvement of taste
Shaping / cutting
The die hole geometry is crucial in the process, as the hot melt has to be depressurized, shaped, and cut. A movable cutting device allows the die holes to be controlled and the knives to be exchanged even during the process. Since a considerable volume of moisture is evaporated at this point, hot air addition and a good aspiration system are needed to prevent the extrud-ates from sticking together. Among other things, using special die holes also allows the production of two-colored products, or the simultaneous production of different shapes and colors.
Two-stage drying
The hot and steaming extrudates very rapidly release the free surface moisture to the hot air stream. Once the surface has been dried, the drying action is limited by the diffusion rate inside the pellets, and the air stream can be reduced. Such a multi-stage drying process consists of a hot air conveying system and a fluid-bed dryer, followed by a belt-type or coun-
ter-current dryer. This process allows very fast, gentle, and non-deforming drying to the necessary final moisture content even of soft and sticky products.
Coating / Cooling
Usually, the dried extrudates are coated while still warm directly after the dryer. During this stage, it is possible to add fats, flavorings, attractants, colors, and even powdered ingredients. Depending on the temperature and the specific surface area of the extrudates, up to 12% liquids can be absorbed in the coating drum and the subsequent cooler.
Extrusion of petfood
Petfood processing focuses on the production of feeds for ani-mals with a high emotional value but low economic usefulness. Nonetheless, balancing the components and gentle processing are at the center of the related quality considerations. Extrusion is therefore increasingly proving to be the right tool for modern Petfood.
Extrusion process
In the extrusion process, a cooking operation follows the spe-cific processing of the raw materials by blending, mixing and grinding. The goal is essentially to achieve the following effects:
• Modification the starch
• Denaturation of proteins
• Shaping, expansion, texturing
• Improvement of taste
Shaping / cutting
The die hole geometry is crucial in the process, as the hot melt has to be depressurized, shaped, and cut. A movable cutting device allows the die holes to be controlled and the knives to be exchanged even during the process. Since a considerable volume of moisture is evaporated at this point, hot air addition and a good aspiration system are needed to prevent the extrud-ates from sticking together. Among other things, using special die holes also allows the production of two-colored products, or the simultaneous production of different shapes and colors.
Two-stage drying
The hot and steaming extrudates very rapidly release the free surface moisture to the hot air stream. Once the surface has been dried, the drying action is limited by the diffusion rate inside the pellets, and the air stream can be reduced. Such a multi-stage drying process consists of a hot air conveying system and a fluid-bed dryer, followed by a belt-type or coun-
ter-current dryer. This process allows very fast, gentle, and non-deforming drying to the necessary final moisture content even of soft and sticky products.
Coating / Cooling
Usually, the dried extrudates are coated while still warm directly after the dryer. During this stage, it is possible to add fats, flavorings, attractants, colors, and even powdered ingredients. Depending on the temperature and the specific surface area of the extrudates, up to 12% liquids can be absorbed in the coating drum and the subsequent cooler.
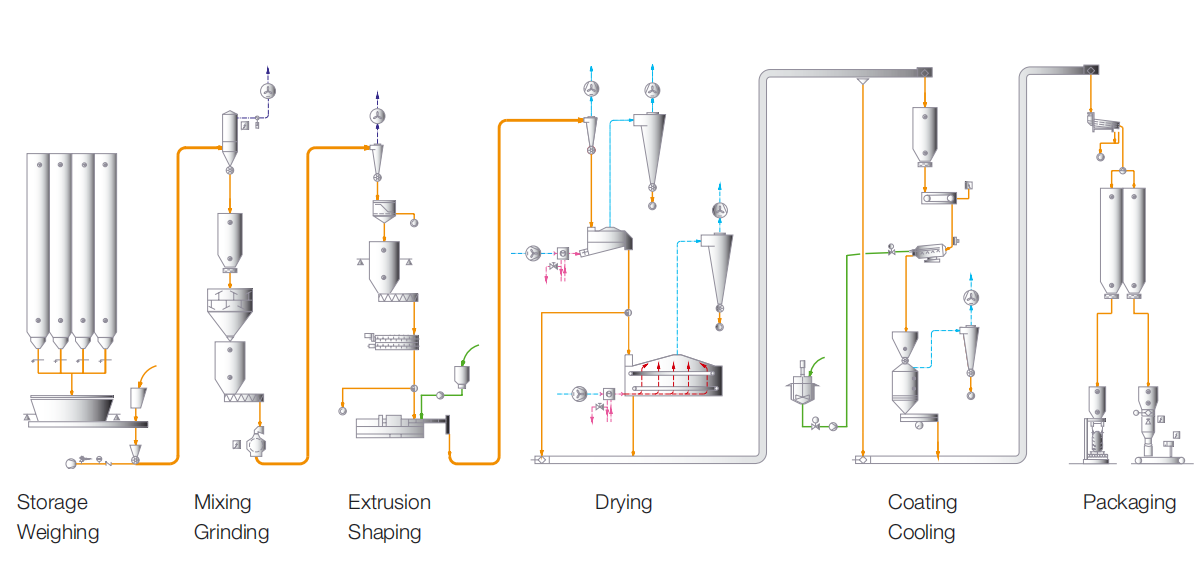